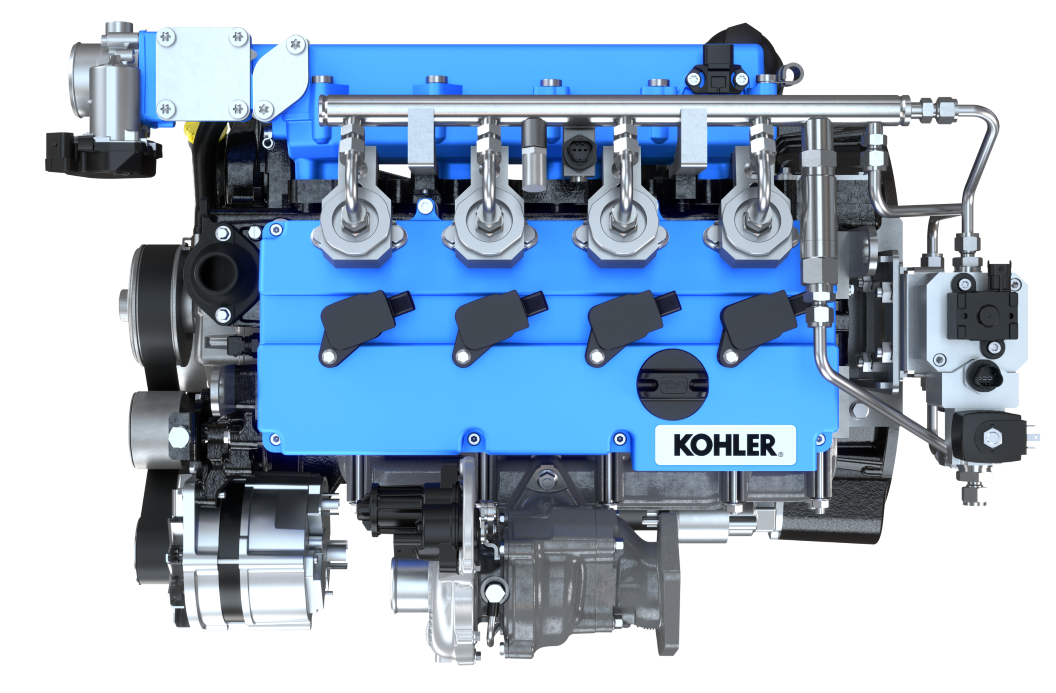
The new hydrogen engine technology is being used in the KDI 2504 TCR unit. This takes advantage of conventional combustion engine architecture and maintains the same dimensions, PTOs and performance as conventional diesel engines, while using zero-carbon hydrogen as fuel.
Kohler Engines is investing in a range of innovative technologies to meet diverse machinery requirements. Hydrogen has emerged as a versatile fuel with rapidly evolving technology. Renowned for its wide flammability range, high flame speed, low ignition energy, and high diffusivity, hydrogen holds promise as a cleaner alternate fuel for internal combustion engines.
Using direct injection (DI) technology, as opposed to port fuel injection (PFI), ensures performance, by avoiding backfiring. The hydrogen unit aims to provide the same performance as the diesel engine, such as max power, peak and low-end torque, as well as transient response and drivability.
Hydrogen plays a pivotal role in emissions and GHG reduction as it offers clean and efficient energy, without generating carbon dioxide (CO2).
The combustion of a hydrogen engine is cleaner than a standard diesel engine and with an aftertreatment system (ATS), the environmental benefits of using hydrogen are increased. Using the ATS ensures the reduction of exhaust emissions to low values, making the engine near zero-emissions. The ATS reduces particulate matter (PM), nitrogen oxides (NOx) and hydrocarbons (HC) to minimal levels.
The hydrogen internal combustion engine is designed to be a drop-in solution, and no major changes to the engine compartment will be required. The engine platform of the machine will keep the same cooling circuit, power take-off and flywheel, engine mounting points, and intake line; in addition, the exhaust line does not need ATS in Stage 5.